Established in 1992 with a registered capital of $5.2 million USD from Australian sole-ownership enterprises, and boasts a 72,000 square meter factory zone. - Custom Injection Molding Machine Manufacturers
Two Weights Prefrom Hot Runner Sharing Mold
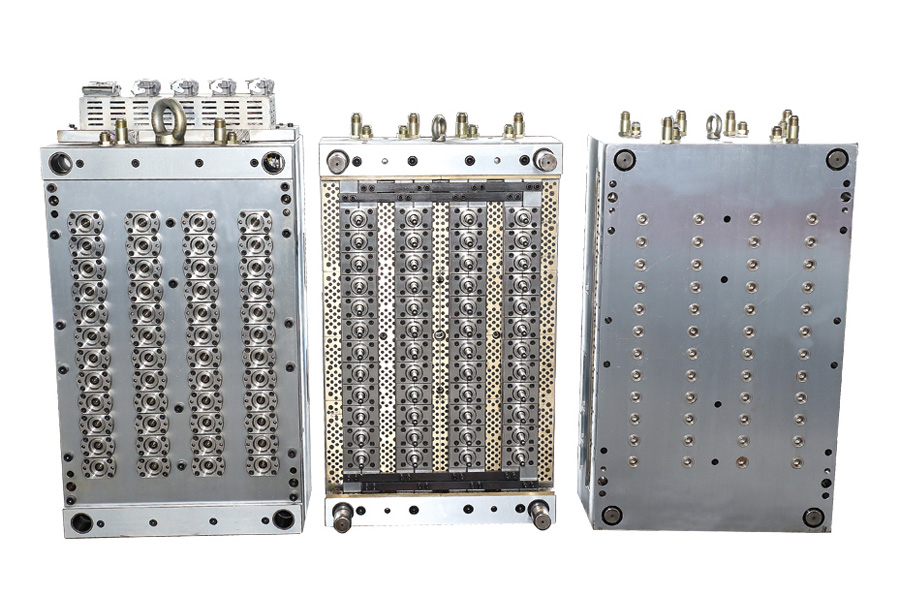
In the case of multi-cavity molds, the size of the preform mold has to be increased. This is done to accommodate the slides and mechanisms in the mold. In addition, the size of the mould must be adjusted to accommodate the transition region of the preform. This is an important step because this region is the area where the product meets the threaded insert.Designed for shaping PET into finished products, a preform mould is a form used to produce PET containers. It is usually made of plain carbon steel or alloy steel. It is hardened to provide a hard surface for the finished product. It can be manufactured in either an injection molding or blow molding process.An important component of a PET preform mould is the insulation plate. The insulation plate should be designed to support high pressure and be able to withstand the stress of the molding process.
The insulation plate should be 12 mm thick.A preform mould can be designed to allow for a variety of features. One such feature is in-mold decorating. In-mold decorating refers to adding a visual element to a part.During hold time for preform mold, cooling is a crucial step in the production of a plastic part. The proper cooling process will increase the production efficiency of the injection molding process. In addition, it can reduce the cost of producing molded plastic parts.Several variables are involved in determining the proper cooling time. These variables include the quality of the material, the temperature of the melt, and the hold time for the preform mold. A mathematical calculation can help determine the appropriate time for the cooling process. If you are unsure of the proper time to cool the preform, a chart should be used as a starting point. The chart can be found in the Reference section.The appropriate cooling time can be calculated by plugging the thermal diffusivity of the material into the proper equation. This equation is similar to the cooling time equation except that it includes the temperature of the melt and the hold time for the preform mold.
Generally speaking, plastics preform moulds and PET preform moulding are two kinds of molds used to make injection preforms. In PET preform moulding, a preform is encased in a molten plastic. This mould is usually shaped like a bottle.The shape of the mold affects the final product. Injection molding is a process that uses pressure to change the fluidity of melted plastic. Optimal molding conditions include injection pressure, injection speed, temperature and gas venting. In PET preform moulding, the flow of melted material is mainly affected by pressure.Optimal temperature is important because it can affect the crystallinity of melt. If the temperature is too high, the plastic may have a poor color. But if the temperature is too low, the material may become opaque.Various types of preform molds are used for manufacturing of plastic products. In fact, they are used in virtually all manufacturing sectors. They are made of alloy steels that provide compression strength and hard surfaces.