Established in 1992 with a registered capital of $5.2 million USD from Australian sole-ownership enterprises, and boasts a 72,000 square meter factory zone. - Custom Injection Molding Machine Manufacturers
(1) Requirements for mold parting surface design
Structural Design of Extrusion Blow Molding Mould The position of the parting surface of the mold should be selected to make the mold symmetrical, reduce the inflation ratio, and facilitate the demoulding of the product. Therefore, the position of the parting surface is usually determined by the shape of the blow molding cavity. Most blow molds are designed as two half-molds that cooperate with the parting surface. For bottles and containers with irregular shapes, the determination of the position of the parting surface is particularly important. Improper position will result in the product being unable to be demolded. Or cause the bottle to be scratched. At this time, it is necessary to use a mold with an irregular parting surface, and sometimes even a multi-parting surface mold composed of three or more movable parts, which is conducive to product demoulding. For a container with a circular cross-section, the parting surface is set through the diameter; for an elliptical container, the parting surface should pass through the long axis of the ellipse; the parting surface of a rectangular volume can pass through the center line or the diagonal line, the latter of which The blow-up ratio can be reduced, but the wall thickness at the corner opposite to the parting surface is smaller. For some products, multiple parting surfaces need to be set. The container handle should be located along the parting surface. The cross-section of the handle should be square, and the corners should be transitioned with arcs to optimize the wall thickness distribution. The handle holes are generally formed by inserts. The handle can also be molded separately by injection molding.
1 Cavity Automatic Blowing Mold
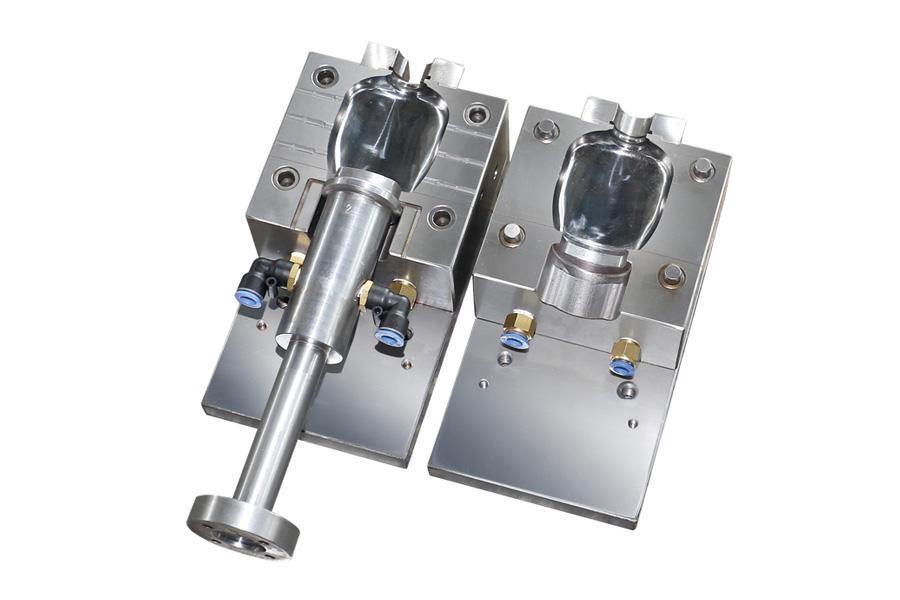
1 Cavity Automatic Blowing Mold
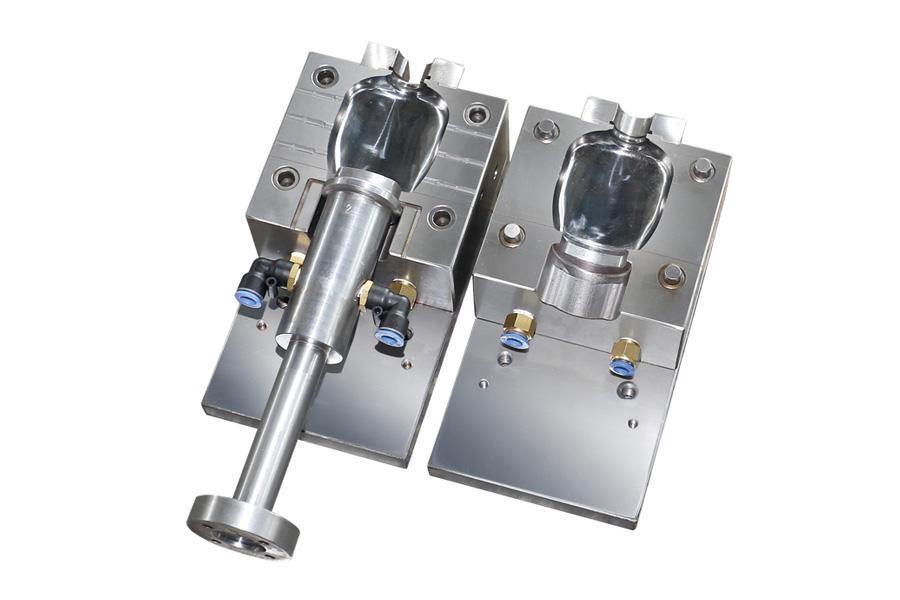
(2) Design requirements of the cavity
The blow mold cavity directly determines the shape, size and appearance of the product. The surface of the mold cavity for PE blow molding should be slightly rough. Otherwise, it will cause the mold cavity to be poorly vented, trapped in air bubbles, and make the product appear "orange peel" surface defects. It also results in a low and non-uniform cooling rate of the product, resulting in different shrinkage rates throughout the product. Due to the low temperature of the PE blow mold and the small inflation pressure of the parison, the inflated parison will not be wedged into the trough of the rough cavity surface, but will be located at or across the crest of the wave, thus ensuring that the product has Smooth surface and provides tiny mesh channels for easy venting of the mold cavity. Sandblasting the cavity can create a rough surface. The sandblasting particle size should be appropriate. For HDPE blow molding molds, a coarser particle size can be used, and LDPE should use a finer particle size. Etching the cavity can also form a rough surface, and can also form patterns on the surface of the product. When blow molding highly transparent or high gloss containers (especially PET, PVC or PP), polish the cavity. For the blow molding of engineering plastics, the mold cavity generally cannot be sandblasted. In addition to etching patterns, it can also be polished or matted.