Established in 1992 with a registered capital of $5.2 million USD from Australian sole-ownership enterprises, and boasts a 72,000 square meter factory zone. - Custom Injection Molding Machine Manufacturers
The all-electric injection molding machine is mainly used for processing waste plastic films (industrial packaging films, agricultural plastic films, greenhouse films, beer bags, handbags, woven bags, agricultural convenience bags, pots, barrels, beverage bottles, furniture, daily necessities, etc.). The all-electric injection molding machine is a widely used and popular plastic recycling machine in the waste plastic recycling industry.
CSD-LP High Speed Automatic Blow Molding Machine
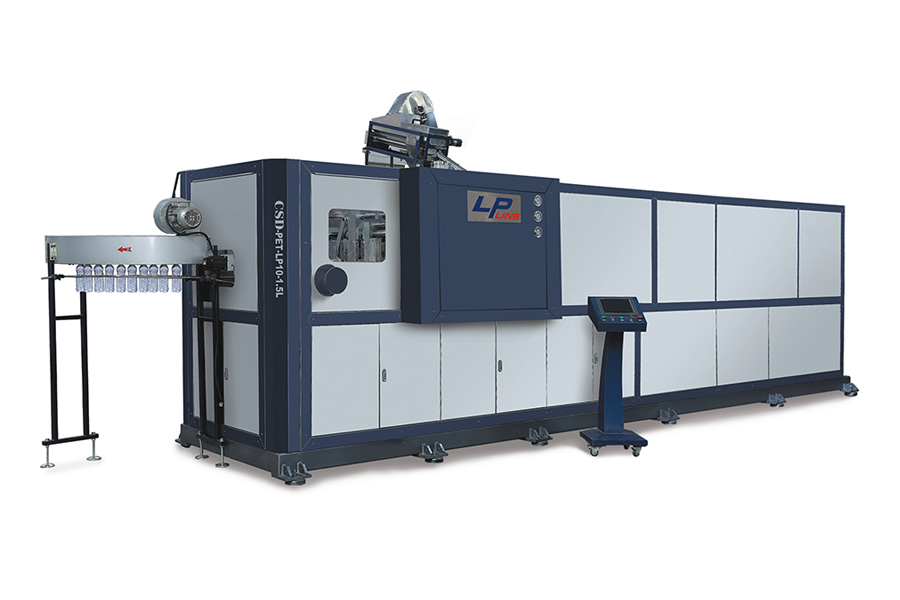
CSD-LP High Speed Automatic Blow Molding Machine
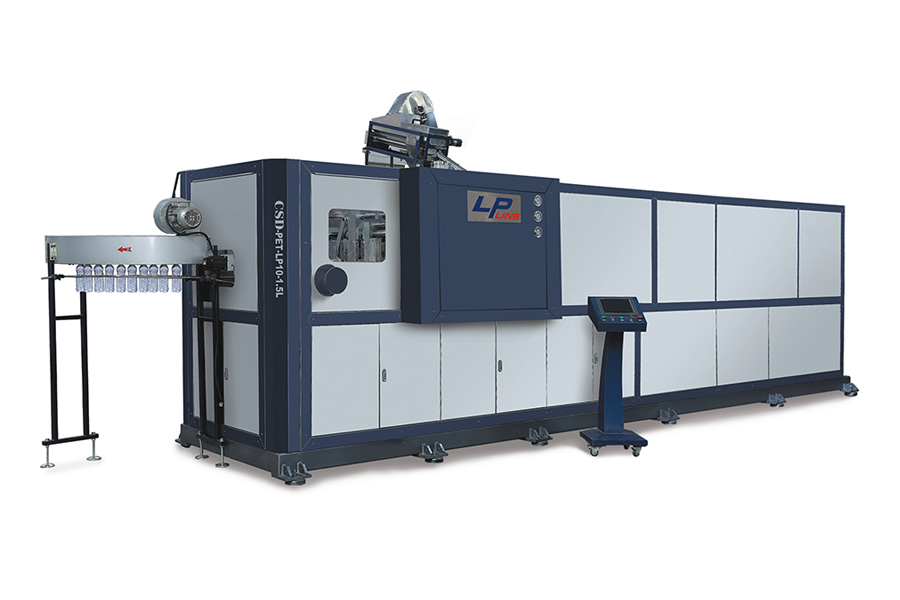
Minimum cost of material and lowestenergy consumption
CSD-LP High Speed Automatic Blow Molding Machine is for producing PP plastic bottles. With over 40 years of experience and outstanding performance, it has become one of the most famous production lines in world market. This machine can be used to produce 500ml, 600ml, 1L, 1.5L, 2L PET preforms with 28-30mm neck which match most common bottle sizes for water beverage as well as cosmetic and pharmaceutical industries. It is well known for its reliable quality and high productivity which is used in factories all over the world
Full Electric Injection Molding Machine Features:
1. After all plastics are sorted, crushed and cleaned, they can be produced, dry, wet but not dry, not dry, not dry.
2. Separation, cleaning, feeding and making pellets from raw materials are automatic.
3. The all-electric injection molding machine makes full use of the high-pressure friction uninterrupted heating system for automatic heating production, avoiding continuous heating and saving electricity and energy.
4. The electromechanical separation of the all-electric injection molding machine is easy to operate.
5. The spiral cylinder is made of carbon structural steel.
6. The appearance of the all-electric injection molding machine is beautiful and elegant, and it can be painted in color according to customer requirements.
Full Electric Injection Molding Machine Maintenance
1. Impurities are not allowed to enter the hopper and barrel, and hard materials such as metal, sand, stone, etc. are strictly prohibited from entering the hopper and barrel.
2. The preheating time should be sufficient. Generally, when the set temperature is reached, the temperature should be kept constant for 15 minutes. Before driving, the manual drive pulley should be light.
3. The screw of the all-electric injection molding machine can only be started at a low speed, and the idling time should not exceed 2 minutes. After feeding, the feeding speed can be gradually increased.
4. The new reducer runs for 500 hours and needs to be replaced with new oil. The quality of the oil should be checked regularly in future use. For oil mixed with impurities or aging, it needs to be replaced at any time. At the same time, the oil level below the specified height needs to be replenished in time. From the next time, the reducer should change the oil every 3000 hours.
5. The screw of the lifting mechanism of the all-electric injection molding machine is filled with low-temperature grease before leaving the factory, and then wiped once a week to replenish the grease.
6. When the main motor is a DC motor, the motor brush should be checked once a month, the record is good, and the carbon brush should be replaced when necessary.
7. The electronic control cabinet should be cleaned once a month.
8. The all-electric injection molding machine checks the wear of the screw and cylinder once a quarter, and has a good record.
9. Check the gears, bearings and oil seals of the gearbox every year.
10. The all-electric injection molding machine should be checked every day, including the lubrication of each lubricating part, the temperature rise and noise of the bearings of each rotating part, the vibration of the unit, the current and voltage display of the motor and electric heater, the temperature of lubricating cooling water, and extrusion products quality etc.
11. When the machine is shut down for a long time, anti-rust and anti-fouling measures should be taken.