Established in 1992 with a registered capital of $5.2 million USD from Australian sole-ownership enterprises, and boasts a 72,000 square meter factory zone. - Custom Injection Molding Machine Manufacturers
12 Cavity Hot Runner Folding fork Mold
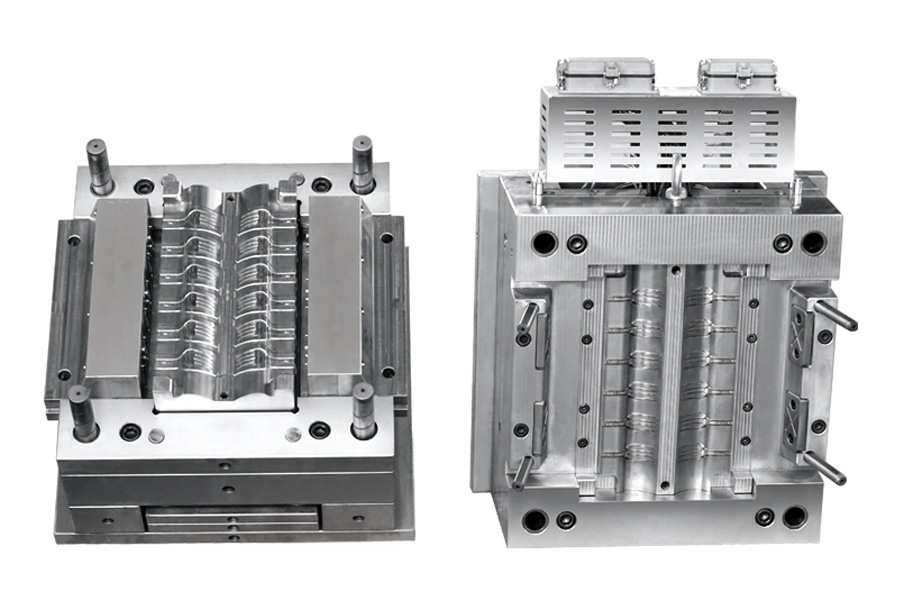
The market share of injection molding machine bottle caps is gradually expanding, and with the increasing appearance demand of customers, the effect of bottle caps is not only reflected in the sealing, but they pay more and more attention to the appearance of the product, such as shape, beauty, finish, etc. Then it is bound to have an impact on the production technology of bottle caps. If the production efficiency is improved while ensuring the quality, it has become a technical problem in the production of bottle cap molds. The suction machine sucks the mixed materials into the barrel of the injection molding machine, heats the barrel to a molten and plasticized state, injects it into the mold cavity, cools and shapes in the cavity, demolds it, and then cuts the ring to add a pad.
After the injection molding production is completed, this is the production process of the injection molding cover. Then cooling and setting have become an important part of affecting the molding time of injection products. The cooling water circuit is an important part of the mold. The quality of the caps and the speed are mostly determined by the cooling water. In traditional mold making, the cooling water channel is generally processed by CNC, and the cooling water channel can only be processed by the milling machine drilling method to generate the internal water channel network, and the water channel flow direction is adjusted by the built-in water stopper and the external plug. In this way, the placement of the waterway has great limitations.
The waterway can only be a cylindrical straight hole, which cannot be rotated around the inner cavity of the mold. When encountering mold products with complex shapes, the traditional waterway cannot be close to the surface of the injection molded parts, the cooling power is low and the cooling is uneven, resulting in a long injection molding cycle and a large amount of product deformation. At the beginning of the production of plastic caps and claw caps such as beverages, the traditional waterway could still be used, but as the product packaging became more complex, the shape of the bottle cap became more and more unique, and the shape was uneven, resulting in the traditional waterway. The cooling effect is stretched.