Established in 1992 with a registered capital of $5.2 million USD from Australian sole-ownership enterprises, and boasts a 72,000 square meter factory zone. - Custom Injection Molding Machine Manufacturers
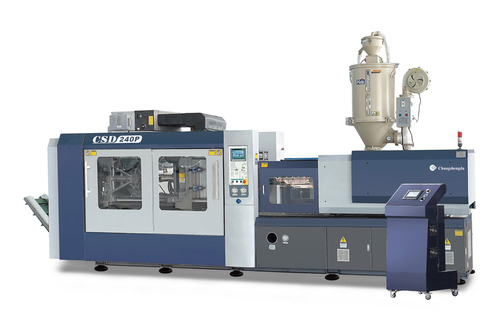
Furthermore, the heated gas manifold lies stationary with respect to the injection patterned die plate. Die clamps and bolts are used to mount the injection panel die stationary plate to the horizontal table, and the blow mold die set is mounted in a similar fashion to the injection panel.Mold markings are plated in the top half and upper half of injection parison dies with holding screws and keyways, and the upper half of injection parison die plates are bolted to the movable clamp that can be moved upward to open as well as downward to clamp.The system is used at the injection and blow molding stations. There is a separate clamp station for injection and blow molding on some injection blow molding machines. The injection station and the blow mold station are not separated clamps on other machines. They use only the same horizontal moving platen. A movable platen on which is mounted the upper half of both the parison injection mold and the upper half of the blow mold which are both mounted to the upper die plate.If a three or four station machine, it would raise and rotate either for a four station machine or for a three station machine after the injection parison mold and the blow mold have opened to their set opening.
The rotating table returns to its starting height and the injection pin clamp and the blow mold clamps close after the rotation has been completed. In this system, the heated particulate is captured and blown off the core rod, while a new particulate is injected into the cavity.The heated thermoplastic parison is lifted off the metal core rod by the rotating horizontal table, and is molded on the plastic inside of the closed blow mold cavity by air or some other gas. Finish, or threaded portions of the parison that are formed at injection parison stations are not blown out of the blow mold tooling, but are held in the blow mold tooling to preserve their design dimensions. By using blow air pressure, only the injected portion is blown off the metal core rod.By blow molding, the moldeable product is cooled after it is formed, so that its dimensions and shape remain the same. The clamps open vertically after the blown product has cooled properly and the parison injection molding has been completed. The horizontal rotating table then rises to its predetermined set position, rotates either 90° or 120°, and carries the new injection molded parison to the blow mold station, the blown product to the strip or eject station, and the core rods free of product to the parison inject station.
Once the horizontal rotating table reaches its predetermined position, it drops vertically downward. The parison inject clamp, blow mold clamp, and stripper all close automatically when this takes place, enabling the formed product to be packaged or strewed into position for secondary operations like decorating, assembly, and treatment. It is now the end of the process.Using a triple-station injection blow molding machine, this procedure is continuously repeated. As an example, a four-station injection blow molding machine could be equipped with a safety check of the core rods at the fourth station to ensure they are clean and free of any product, or an air chamber that would condition the core rods. For machines capable of blowing polyethylene terephthalate or polyethylene naphthalate-based containers, this holds particularly true. During the fourth station, the blown containers can also be flame heated and decorated. We will discuss condition and decoration more extensively in the chapter on processing.