Established in 1992 with a registered capital of $5.2 million USD from Australian sole-ownership enterprises, and boasts a 72,000 square meter factory zone. - Custom Injection Molding Machine Manufacturers
CSD-AX1-M-2.5L Automatic Blow Molding Machine
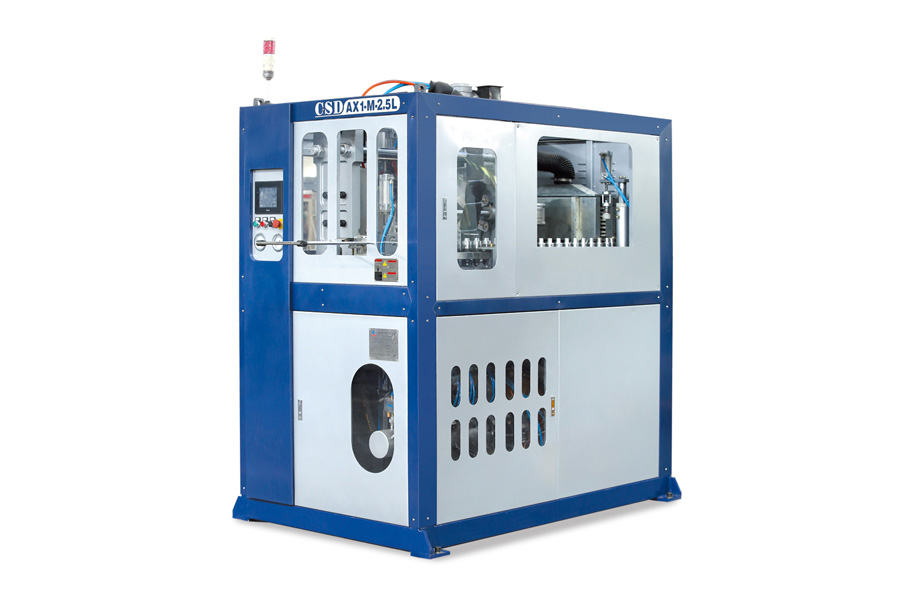
Injection stretch blow molding machines have a variety of uses, and are ideal for manufacturing large quantities of plastic products. They combine two distinct processes for plastic product manufacturing: the injection mold creates the preform, and the blow mold finishes the blowing process. These machines are best used when large volume runs are necessary, such as for producing peanut butter jars, liquor bottles, or water bottles.Injection stretch blow molding machines are available for various industries, including pharmaceuticals, health care, personal care, beauty, and food products. Some of these machines are fully automatic and feature touch screens for quick and easy troubleshooting. They also have a closed loop hydraulic system with proportional pressure and flow rate control.Moreover, these machines are designed with an angular index device for mold seating.Injection stretch blow molding machines are used to produce high-quality containers. After a pre-blow cycle, the polymer flows into the injection cavity via a hot runner block.
The injection moulding machine then creates the part with a pre-determined outer diameter. Once the injection moulding process has completed, the preform is held in a neck carrier. It is then conditioned to the proper temperature and is ready for BLOWING and stretching. In this process, the stretch rod is introduced to stretch the preform longitudinally. Two levels of air pressure are then used to blow the preform circumferentially.There are various types of blow molding machines available in the market. Injection blow molding machines are usually used for the creation of plastic objects. These machines use air pressure and heat to melt the plastic material. After cooling, the melted plastic is ejected from the machine. These machines can produce a variety of plastic products, including milk jugs, shampoo bottles, and various automotive parts.Plastic is one of the most popular materials used in the manufacturing process. It can be used for a variety of products, including milk or water bottles, shampoo bottles, and jerry cans. It is also used to manufacture automotive parts like air ducts.
However, there are some limitations when it comes to plastic bottles.The basic components of a blow molding machine include an extruder. The extruder is a component that melts plastic under pressure and then pushes it forward into the mold. The machine also includes a mold, which is a metal shape used to produce the finished product. During the manufacturing process, the plastic is melted and cooled into the final part shape.If you are planning to purchase a blow molding machine for your business, there are many different factors to consider. The cost of the machine will depend on the type of product that you will be producing. In general, a single-cavity mold can cost about $3000 to $6000. Multi-cavity molds can cost up to $90,000 or more, depending on the capacity of your machine. The cost will also depend on the type of mold you will need. For example, blow molding is ideal for single-piece hollow molds, while plastic injection molding is more appropriate for large-scale production of highly engineered products.