Established in 1992 with a registered capital of $5.2 million USD from Australian sole-ownership enterprises, and boasts a 72,000 square meter factory zone. - Custom Injection Molding Machine Manufacturers
CSD-AB Automatic Blow Molding Machine(Up Blow)
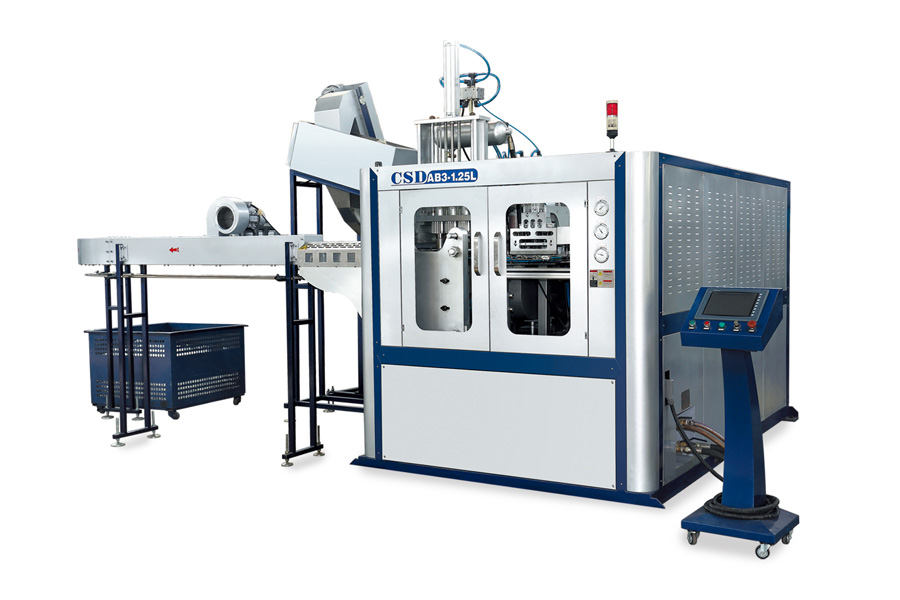
Maximum efficiency in linear blowing
The max diameter of product is Φ120,Φ90 and the neck size product is Φ15-Φ38. The usefull area of mould plate is 350×350 or 520×350,880×400 or 480×400 or 620×460. Max mould thickness is 220,220 or 258mm ,min mould thickness 180 mm.They have clamping force 120,710 or 210KN and stretching stroke 350,350 or 350mm. The working pressure is 0.8-1.0Mpa and blowing air pressure 2.6-3Mpa
Downblow is the most commonly used blow-molding method. Our engineers have designed the CSD-AB to be a completely automatic blow molding machine, which consists of vibration unit, injection unit, gate trimming unit and re-straining unit. The machine is able to work with different mould dies and has high production efficiency. The machine uses lifting air pressure and down blow blowing air pressure to form plastic products. It can work on PVC, PP, PE with light weight material and semi-heavy weight material.
Using a preform mold to manufacture a plastic injection molded part can produce a product that's barely noticeable when you examine the finished article. A well made mold can last a lifetime and is well worth the price tag. To keep the mold in tip top shape, a regular maintenance program is recommended. To minimize wear and tear, a small change to the mold's geometry can produce excellent results.A properly set up mold can be a boon to any shop's bottom line. A properly aligned mold can eliminate part shrinkage allowing for a more aesthetically pleasing product. The proper configuration of ribs and bosses near corners will help reduce the stress associated with a sag prone part. A good mold will also help keep a product's design integrity intact.Unlike the likes of a well heeled executive, a high schooler in the doldrums might be able to snuff the lowball.
As such, the best suited apex prince will be a high school sleuth on high alert. To keep the adolescent at bay, a little oomph and a little oomph is needed. Fortunately, Novapet is a jack of all trades and all disciplines. Having said that, the company has been in the business of making rPET since its inception in the mid 1980's, a feat of sexiest proportions if you ask me. The company's eponymous rPET brand is the gold standard in the rPET business sphere, as a result of its nifty little operation. The company has a plethora of aforementioned rPET projects in the pipeline.XFORM is a 500 ton machine that's capable of producing over 140,000 preforms an hour. It also has a number of high-tech features to keep your production lines running smoothly. It's not just for pet bottles though, the system can produce a variety of carbonated soft drinks and dairy products. The system can also handle molds of various sizes. It is cost effective and scalable, making it an ideal choice for small and large enterprises alike.The XFORM 500 GEN4 is no slouch in the performance department, boasting a slick servo driven 140 mm extruder with a shot size of 6.0 kg. It also has a second generation high-speed cooling robot for optimal dimensional consistency.
It also has a cleverly designed post-mold cooling system to reduce downtime and operator error. The XFORM also sports a 500 tonne double-toggle clamping unit with an even spread of clamp force to minimize mold wear.Unlike other types of gates, valve gate systems provide a good operating window for preform molds. This is due to their simple construction. They also eliminate the need for auxiliary power systems.Another benefit of valve gate systems is that they can fit into a smaller footprint. This is important in thin wall molding applications, which are characterized by high fill rates and rapid cooling.In addition, they allow for easier pin positioning. They also offer a faster cycle time and less stress on PET preforms. These advantages make them an excellent choice for thin wall molding.A better-designed valve gate system can be installed without adding to the mold base's height or footprint. These types of systems can also reduce operational costs and improve the quality of parts.