Established in 1992 with a registered capital of $5.2 million USD from Australian sole-ownership enterprises, and boasts a 72,000 square meter factory zone. - Custom Injection Molding Machine Manufacturers
1 Cavity Automatic Blowing Mold
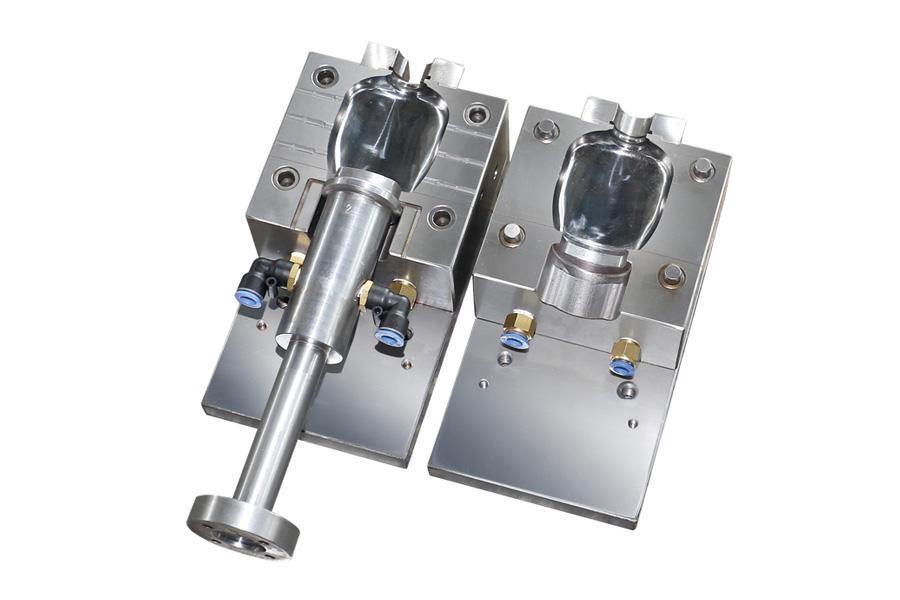
To ensure the proper flow of the resin, engineers must design the mold properly. They also have to consider the length and diameter of the runner.Runners are especially important in multi-cavity molds. Having shorter and larger cross sections reduces pressure loss and helps in reducing mold size.When designing a plastic molding system, there are several important factors to consider. These include the type of gate system used, the size of the melt channel, the design of the cold material well, and the temperature of the mold feed. In addition, the injection pressure of the ram of an injection machine plays an important role in the flow of the plastic melt.It is important to understand the flow of resin because it will affect the final product. One of the easiest ways to do this is to use a simulation tool. This is especially important for materials with poor melt-flow performance.
A mold flow simulation will help you determine the proper injection pressure. You should also consider the material's temperature, viscosity, and shear. All these factors can affect the strength of the molded part.When it comes to the design of the cold material well, it is important to choose a well that is appropriate for the size of the product. Also, you should choose a design that minimizes pressure drops.Choosing the right size plastic mold is important for a variety of reasons. It plays a key role in overall cost and production time. Typically, it's best to choose a mold that fits within the limits of your injection molding equipment. You can do this by taking the time to understand the features and functions of your press.In addition to knowing the size of the machine you'll be using, you'll also want to consider the part's complexity. Complex parts have the potential to require more time and money from your mold maker.
Knowing this will allow you to find the right injection molding partner for your project.The most basic of all plastic injection molds is the straight pull model. These molds are essentially a core that is placed on the back side. This makes it easier to remove, and allows you to minimize cost.You'll also want to consider the location of the gate on the mold. Locating it on the wrong side can lead to uneven product stress and possible warpage.Choosing the right surface texture of a plastic mold can make a big difference in the look, feel, and performance of your product. There are a number of different surface textures to choose from. This article will give you a general overview of the various types.The SPI (Society of Plastics Industry) is a trade organization that sets and maintains standards for surface finishes. These include standard finishing procedures and a variety of surface finish charts.Injection molding is used to create a variety of plastic parts. Parts with textured surfaces are typically more durable and hold paint for longer periods of time. Texturing also makes the part easier to grip.