Established in 1992 with a registered capital of $5.2 million USD from Australian sole-ownership enterprises, and boasts a 72,000 square meter factory zone. - Custom Injection Molding Machine Manufacturers
Preform molds are an essential component of the PET (polyethylene terephthalate) bottle manufacturing process. Preform molds are used to create the preform, which is the starting point for creating PET bottles. Preforms are small, tubular objects made from PET resin that are shaped like test tubes. They are then blown into a bottle using a blow molding machine.
The preform molding process is a critical step in the PET bottle manufacturing process. The quality of the preform molds directly affects the quality of the final product. The preform mold is responsible for shaping the preform into the correct dimensions and ensuring that it is of the correct thickness and weight.
Preform molds come in a variety of sizes and configurations, depending on the size and shape of the bottle being produced. The mold is typically made from high-quality steel and is designed to withstand the high pressures and temperatures of the molding process. The mold is also designed to be durable and long-lasting, as it will be used to produce thousands of preforms over its lifetime.
The preform molding process begins with the injection of molten PET resin into the preform mold. The mold is then cooled to solidify the resin, and the preform is ejected from the mold. The preform is then transferred to a blow molding machine, where it is heated and stretched to form the final bottle.
The preform molding process requires a high degree of precision and accuracy. The mold must be designed to exacting specifications to ensure that the preform is of the correct dimensions and weight. The mold must also be properly maintained to ensure that it continues to produce high-quality preforms over its lifetime.
One of the most important factors in the preform molding process is the design of the mold. The mold must be designed to allow for the correct flow of resin and the correct cooling of the preform. The mold must also be designed to prevent defects such as flash, sink marks, and warpage.
Another important factor in the preform molding process is the quality of the resin used. The resin must be of high quality and free from impurities to ensure that the preform is of the correct quality. The resin must also be properly dried before it is used to prevent moisture from affecting the quality of the preform.
In conclusion, preform molds are a critical component of the PET bottle manufacturing process. The quality of the preform mold directly affects the quality of the final product. The preform molding process requires a high degree of precision and accuracy, and the mold must be designed and maintained to exacting specifications to ensure that it produces high-quality preforms over its lifetime. The use of high-quality resin and proper drying techniques are also essential to ensure that the preform is of the correct quality.
Two Weights Prefrom Hot Runner Sharing Mold
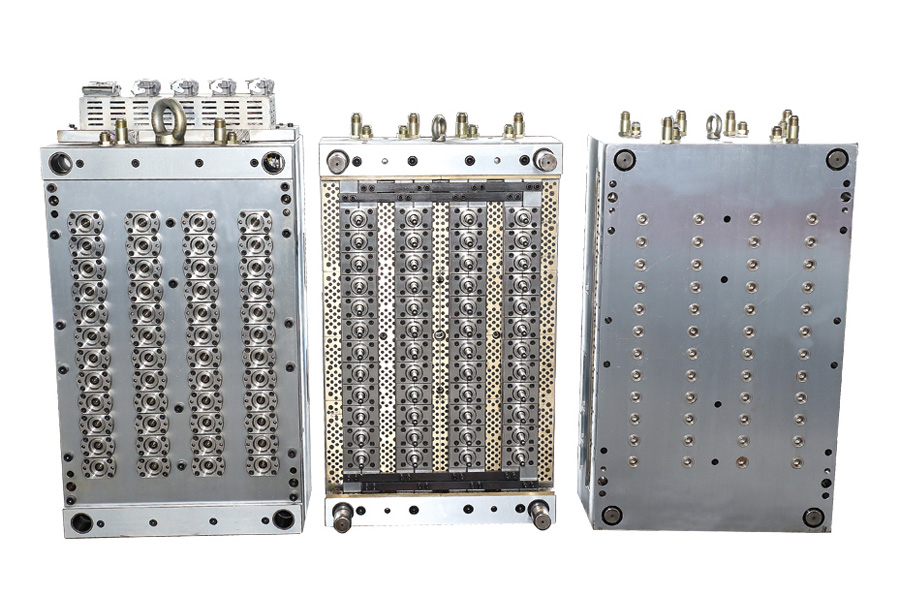